Blog
Danger of contamination
Contamination through seals! A horror for operators of any plant. But how to get a grip on it?
The high hygienic requirements in industry rightly demand cleaning processes that must be ever cleaner and faster.
One would like to counteract the danger of contamination by increasing the temperature or even the concentration of the cleaning agents. Besides, this would also shorten the cleaning time and the system would be ready for operation again sooner – but some components, which are actually of secondary importance, put the brakes on: the seals.
A confusing variety of qualities makes life difficult. How do you know when to use materials like MVQ silicone, NBR, HNBR, FKM, EPDM and why are there actually so many different ones? These rubber parts are quite soft and tend to grow strongly (intrusion) into the pipeline when heavily loaded at the limit, which leads to flow losses and dead spaces that pose an additional contamination risk.
Elastomer seal
- ID Intrusion
- Product accumulation
- Bacteria formation
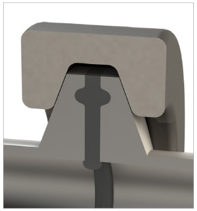
PTFE would be interesting here. It is not a rubber (elastomer), but a harder plastic (plastomer) and almost resistant to all chemicals. Unfortunately, this clever idea dies with PTFE’s own so-called cold flow. If too much force is applied, it flows away in all directions.
Traditional PTFE
- ID recession or intrusion
- Product accumulation
- Bacteria formation
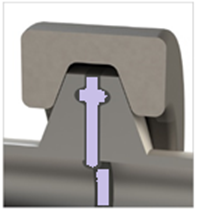
Yet seals would be an important factor in increasing productivity, support the maintenance of hygiene standards and would have a not inconsiderable influence on the economic efficiency of a plant.
What if the cold flow of PTFE could be defeated?
Garlock has already achieved this with its GYLON® material series. GYLON® flat gaskets have already overcome many critical challenges in industry. Among conventional sealing solutions, there are hardly any suitable materials that are resistant to acids and alkalis and can additionally be used at demanding temperatures and pressures.
Elastomers usually fail in at least one of these requirements and conventional PTFE in turn proves unsuitable because of cold flow. So if GYLON® could also be used in other geometries, the idea of a material that can be used for almost all applications would have been brought back to life.
We have thought about, discussed and researched this idea.
The result: GYLON BIO-LINE® for food applications and GYLON BIO-LINE® PLUS for the pharmaceutical sector. GYLON® has proven itself in intensive tests under the toughest conditions in both areas and has become a sought-after material to meet increased plant availability in the future. In addition, the GYLON BIO-LINE® and the GYLON BIO-LINE® PLUS not only ensure safe and economical processes, but also contribute to inventory optimisation.
Stopped cold flow is good, but does this also banish the problem of contamination by rubber of drastically narrowed pipelines?
GYLON BIO-LINE® and GYLON BIO-LINE® PLUS show clear superiority in dimensional stability. Rubber gaskets tend to swell out of joints (extrusion) under mechanical stress due to vibration and misalignment. Extruded rubber seals cause dead spaces that impair cleaning and worsen the sterilisation result. A risk of contamination due to residues on the sealing material is the result. GYLON BIO-LINE® and GYLON BIO-LINE® PLUS gaskets remain flexible, tight and reliably flush with the pipe bore even under high loads.
GYLON BIO-PRO® / GYLON BIO-PRO® PLUS
- Smooth inner diameter
- Easy cleaning
- Dimensional stability
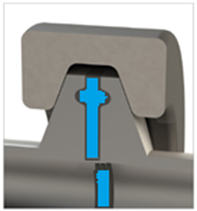
An exaggerated claim? Take a look at the test results:
PTFE SEALINGS: Before and after with 5 Nm torque
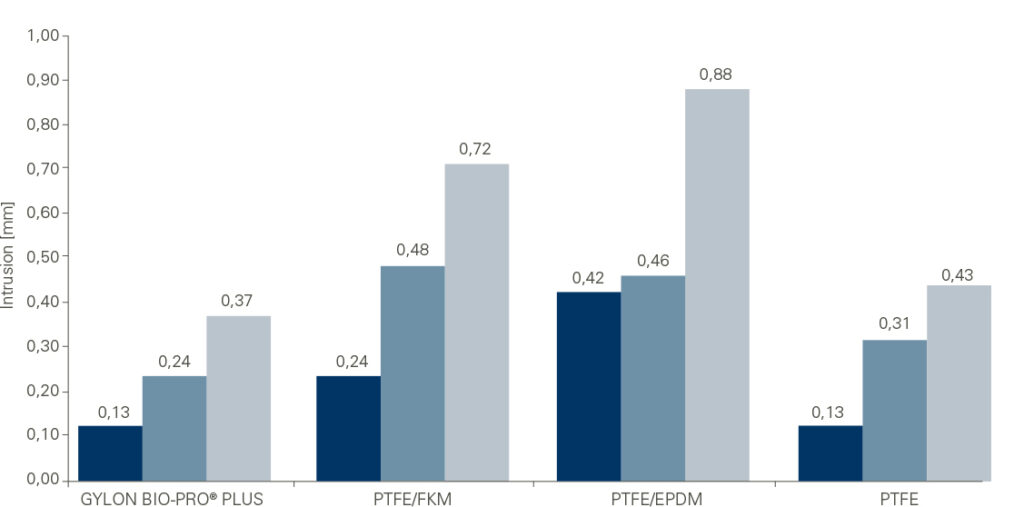
The values given in the illustrations represent the deviations of the measured inner diameters in each case:
- Bar 1 (colour 1): Difference between the original inner diameter of the seal and the inner diameter of the seal after assembly.
- Bar 2 (colour 2): Difference between the inner diameter of the gasket after assembly and the inner diameter of the gasket after exposure to heat in the assembled state.
- Bar 3 (colour 3): Measured total seal intrusion = intrusion assembly + intrusion heat exposure.
ELASTOMER (70° Shore A): Before and after with 3 Nm torque
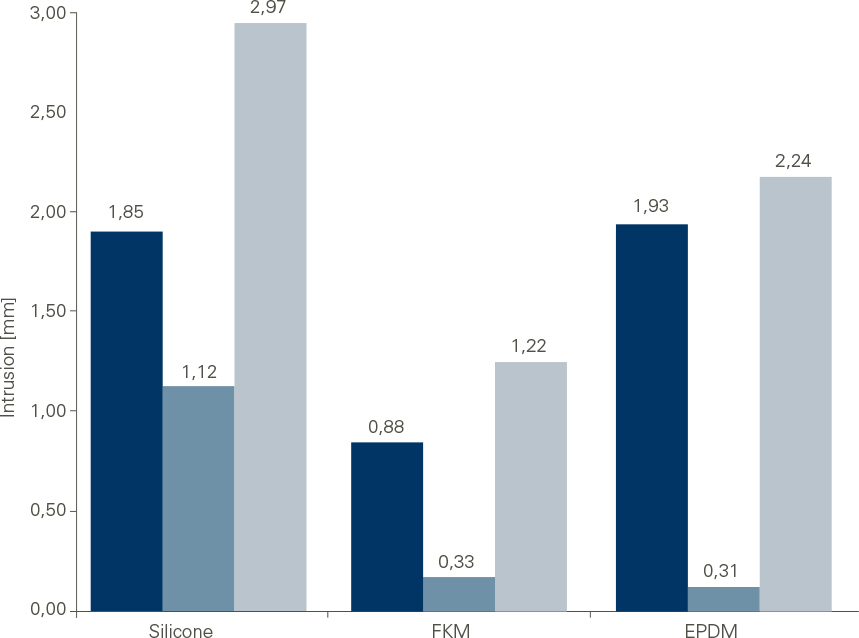
The values given in the illustrations represent the deviations of the measured inner diameters in each case:
- Bar 1 (colour 1): Difference between the original inner diameter of the seal and the inner diameter of the seal after assembly.
- Bar 2 (colour 2): Difference between the inner diameter of the gasket after assembly and the inner diameter of the gasket after exposure to heat in the assembled state.
- Bar 3 (colour 3): Measured total seal intrusion = intrusion assembly + intrusion heat exposure.
The results clearly show that GYLON BIO-PRO® PLUS has a comparatively very low swelling behaviour. In particular, the rubber gaskets and the PTFE/rubber gaskets show relatively high swelling behaviour, both after assembly at room temperature and after exposure to heat.
It was not taken into account that vibrations frequently caused by pumps, for example, can also lead to a loosening of the sealing connection and thus to a leak. Further tightening of the joint creates additional extrusion of the rubber into the pipeline.
If the temperature drops (shutdown of the system) and the rubber contracts as a result, it is torn off in the process. Rubber chunks then metastasise through the entire system. This results in contamination and a high demand for replacement seals.
Wouldn’t you also like to work contamination-free and future-proof in your plant?
Tri-Clamp, milk pipe and aseptic seals from the GYLON BIO-LINE® and GYLON BIO-LINE® PLUS series are available from Garlock and are available in all common standard dimensions (DIN 36676; ISO 2852; BS 4825; ASME-BPE). In addition, their performance is certified and supported in conformity with EC 1935/2004, EC 10/2011, USP Class VI, FDA, etc.
GYLON BIO-LINE® and GYLON BIO-LINE® PLUS – a clean thing.
Garlock GmbH
Falkenweg 1
41468 Neuss
Germany
+49 2131 349-0
garlockgmbh @ garlock.com
© 2025 Garlock GmbH, Germany
An ENPRO Company
www.garlock.com
Garlock Europe Webshop
www.garlock.eu.com
Career Site Europe
www.garlock-karriere.de/en